Research Highlights
研究ハイライト
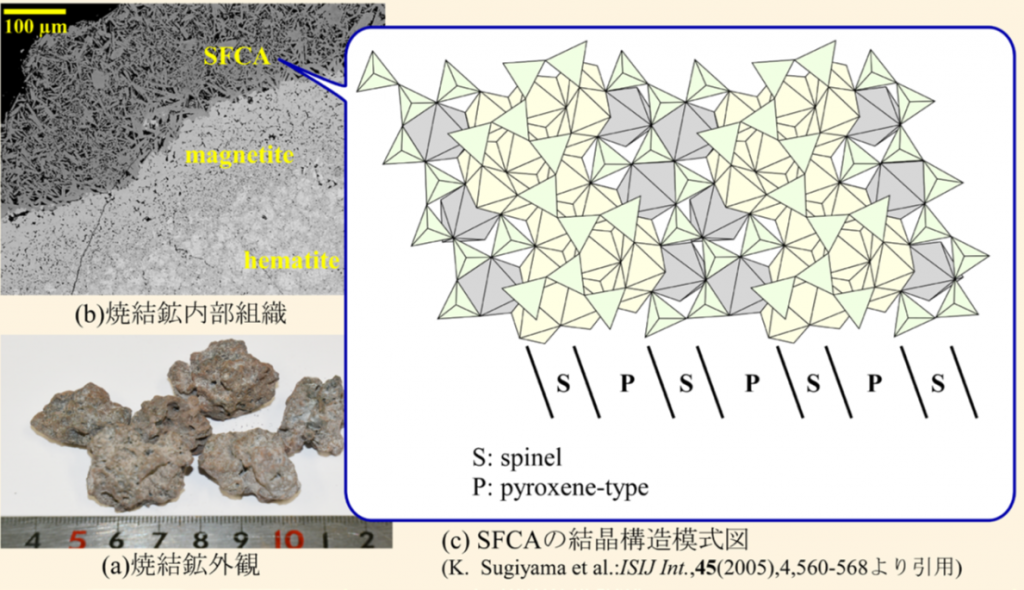
Microstructure and quality of iron ore sinters for hydrogen blast furnace
In order to reduce CO2 emissions in the ironmaking process, it is necessary to produce iron ore sinters that are superior in terms of reducibility and strength. Iron ore sinters are main iron source for blast furnace, which are a mixture of iron ore and limestone and are calcined at high temperatures. Iron ore sinters are mainly composed of hematite (Fe2O3), magnetite (Fe3O4), calcium ferrite, and slag. Among them, the most important phase responsible for the high quality of sinters is needle-shaped multicomponent calcium ferrite (Silico-Ferrite of Calcium and Aluminum, SFCA). SFCA is an oxide solid solution composed of Fe2O3, CaO, Al2O3, SiO2, and MgO with a complex crystal structure as shown in the figure. In addition to SFCA, there are a total of four known crystal structures: SFCA, SFCA-I, SFCA-II, and SFCA-III. However, the single-phase region of these oxide solid solutions and the phase equilibrium relationship have not been clarified yet. The effect of the composition, crystalline structure, and morphology on the reducibility should also be investigated. Then, we are focusing on the following researches:
– Study of phase diagram including the compositional range of the SFCA system
– Effect of composition and crystal structure of SFCA series on the reducibility of SFCA
– Iron oxide activity in the SFCA series
– Microstructures of iron ore sinters suitable for hydrogen blast furnace
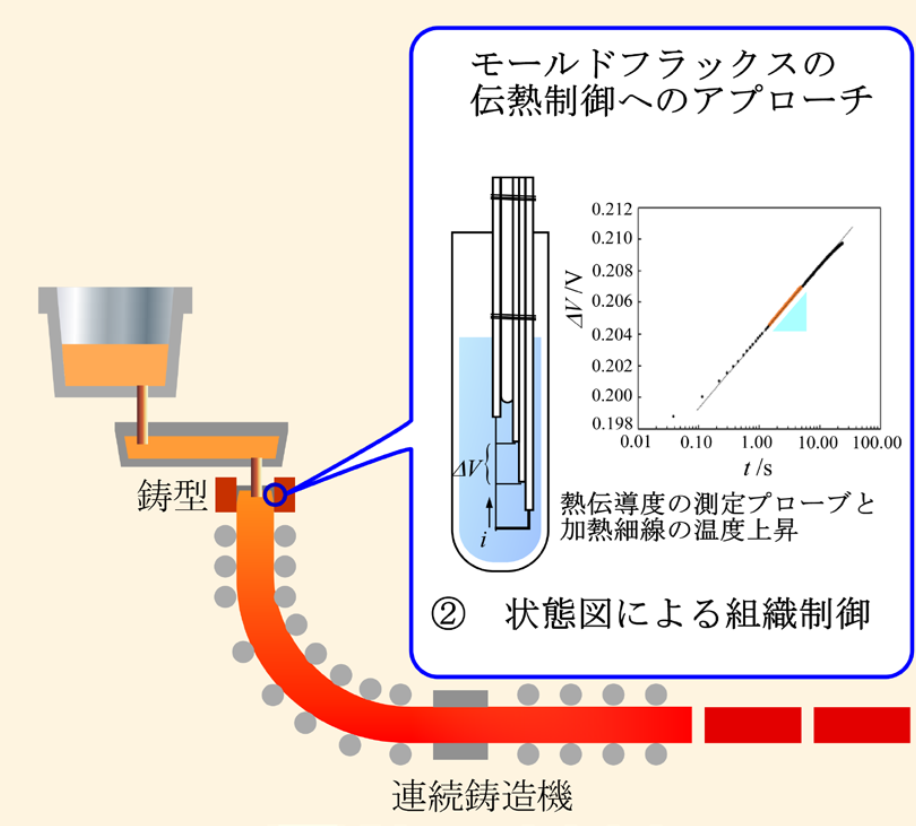
Crystallization and heat transfer of mold flux for continuous casting of steel
In steelmaking, molten steel is refined to a high purity in the refining process and solidified in the continuous casting process. In the continuous casting process, synthetic slag called mold flux is used to maintain lubrication between the steel and mold. Mold flux not only works as a lubricant but also controls the cooling rate of the steel, contributing to the improvement of the quality. Our laboratory is focusing on the following studies related to the crystallization behaviors and thermophysical properties of mold flux to control heat transfer from molten steel to mold.
– Thermal conductivity measurements of crystalline, glassy, and molten slag phases in mold flux
– Phase diagram of mold flux
– Crystallization behavior of mold flux
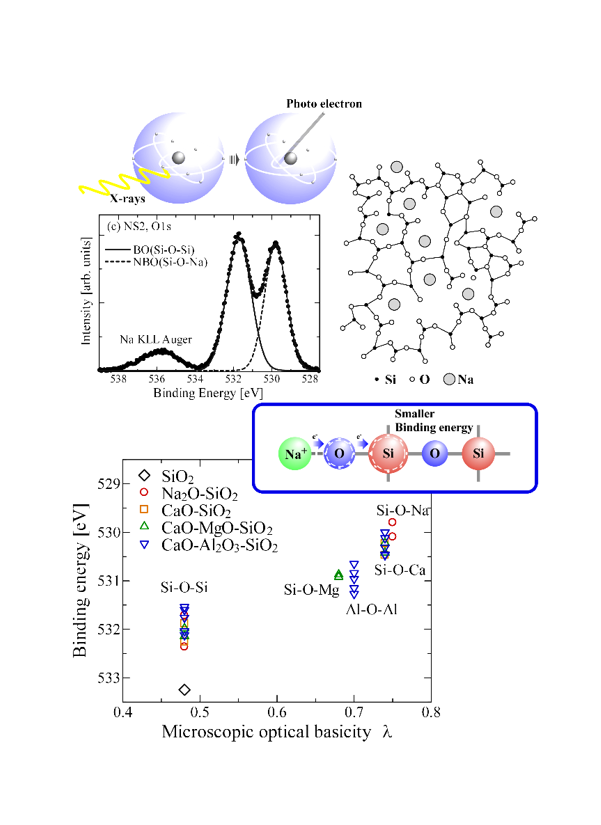
Application of steel slag to cement and geopolymer
Ironmaking process produces a large amount of steel slag as a byproduct. Steel slag can be categorized into two: blast furnace slag and steelmaking slag. Blast furnace slag is used as a raw material for cement, and steelmaking slag is used as a roadbed material and a raw material for iron ore sinter. Blast furnace slag cement does not require calcination of limestone and thus contributes significantly to the reduction of CO2 emissions. In recent years, research and development of an alternative to cement called geopolymer, which is made from blast furnace slag and fly ash, has been promoted. Geopolymer does not require a calcination process and is expected to further reduce CO2 emissions. Our laboratory is pursuing the recyclability of slag from a principled perspective based on the slag structure so that it can be flexibly recycled into cement and geopolymers even if the slag composition changes significantly due to the development of a new process associated with the carbon neutralization of steelmaking.